LEAN SIX SIGMA
Optimising efficiency by minimising waste, cost and process delays.
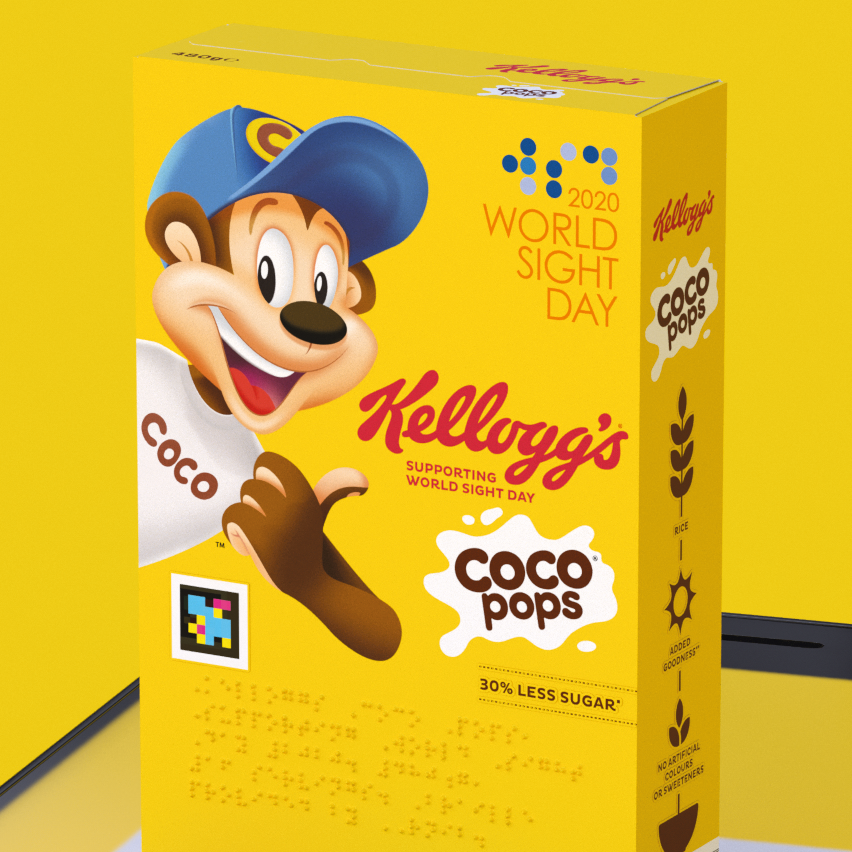
No matter how highly skilled your people are, if your process is inefficient, your team will be too. By fusing the philosophies of Lean and the practical tools of Six Sigma, our experts identify and evaluate the hot spots in your current process that create delays, increase process costs, and don’t add value.
We then create bespoke solutions that address the root cause, without reducing the overall quality. Just some of the reasons why, from Kellogg’s to Quorn, our Lean Six Sigma team is trusted to deliver the best practice process.
A methodical approach to efficiency
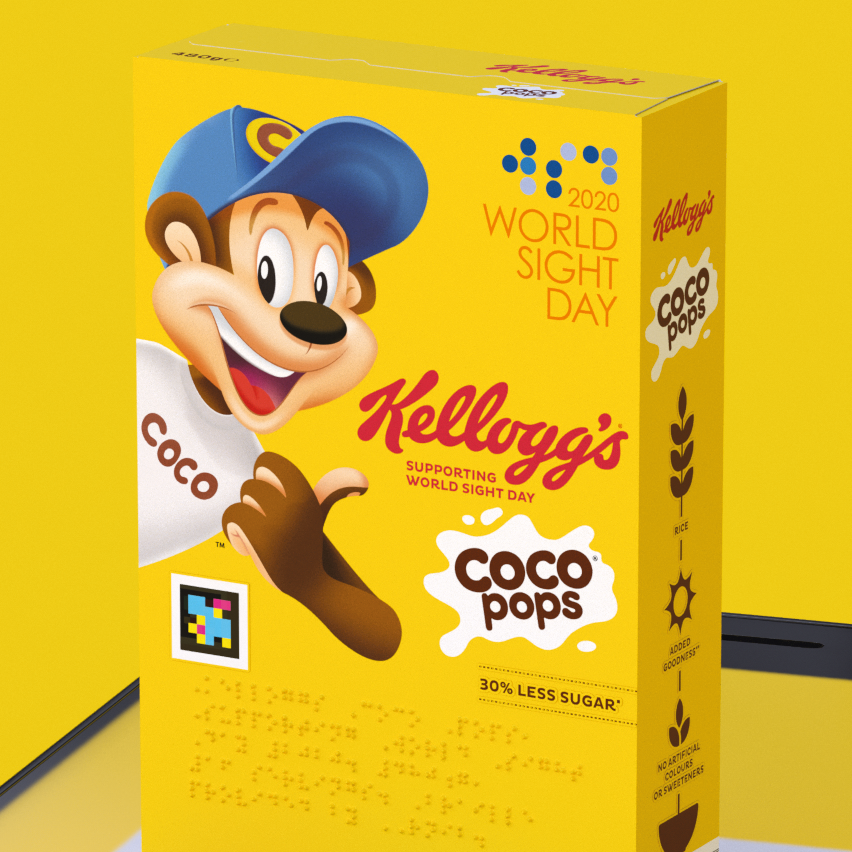
D Define the existing challenge you need to overcome
M Measure the current state ‘as is’
A Analyse the root cause and create the new ‘to be’
I Improve the process by evaluating the solutions
C Control the process to sustain the change
REMOVE WASTE. ADD VALUE.
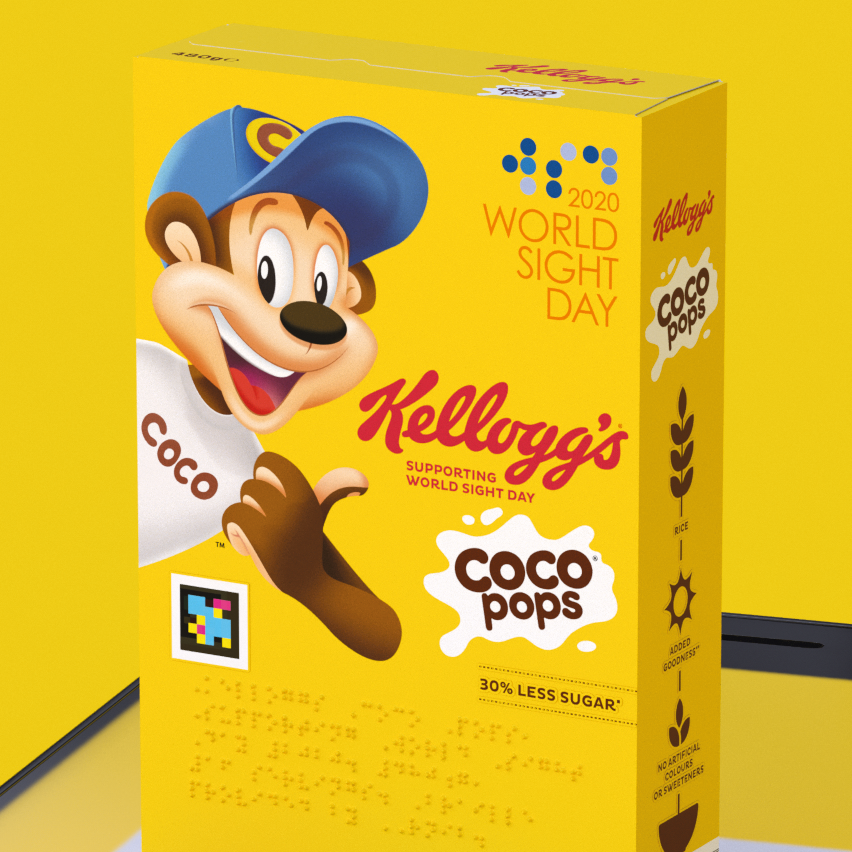
Waiting – address delays in waiting for items or information
Overproduction – identify where work is done before it is needed, or unnecessary
Rework – ensure Right First Time accuracy, every time
Movement/motion – reduce excessive movement with the workspace
Over processing – prevent your team from doing more work or adding more processes than necessary
Over inventory – reduce the number of excess products being processed
Transportation – optimise the movement of items and information
Skills – use your people to their full potential